Belly inflation on industrial processes has become a significant concern for manufacturing sectors worldwide. It refers to the abnormal expansion or bloating of equipment or containers due to excessive internal pressure. This phenomenon can lead to catastrophic failures, endangering lives and causing substantial financial losses. Understanding belly inflation is crucial for ensuring safety, efficiency, and sustainability in industrial operations.
In the modern industrial landscape, where efficiency and productivity are paramount, the risks associated with belly inflation cannot be overlooked. From oil and gas pipelines to chemical storage tanks, any equipment that handles pressurized materials is susceptible to this issue. As industries continue to evolve, so does the need for comprehensive knowledge about belly inflation and its prevention.
This article aims to provide an in-depth exploration of belly inflation on industrial systems. By examining its causes, effects, and mitigation strategies, we hope to equip professionals and enthusiasts with the tools necessary to address this critical challenge. Let's dive into the details and uncover how belly inflation impacts the industrial sector.
Read also:The Dew Boys Unveiling The Phenomenon In Music And Pop Culture
Table of Contents
- Introduction to Belly Inflation
- Causes of Belly Inflation
- Effects on Industrial Systems
- Prevention and Mitigation
- Technological Advancements
- Industrial Case Studies
- Regulatory Standards
- Economic Impact
- Safety Protocols
- Future Trends
Introduction to Belly Inflation
Belly inflation on industrial equipment occurs when internal pressure exceeds the design limits of the system, causing deformation or swelling. This phenomenon is particularly prevalent in pipelines, storage tanks, and pressure vessels. The consequences of belly inflation can range from minor operational disruptions to severe accidents, making it a priority for industrial safety experts.
What is Belly Inflation?
Belly inflation refers to the physical expansion of industrial components due to excessive internal pressure. This can lead to permanent deformation, material fatigue, and eventual failure. Understanding the mechanisms behind belly inflation is essential for developing effective prevention strategies.
Why is Belly Inflation a Concern?
The primary concern with belly inflation lies in its potential to cause catastrophic failures. Such failures can result in leaks, explosions, and environmental damage, posing significant risks to human life and property. Industries must therefore remain vigilant in monitoring and addressing this issue.
Causes of Belly Inflation
Several factors contribute to belly inflation on industrial systems. These include design flaws, material degradation, and operational errors. Identifying these causes is the first step toward mitigating the risks associated with belly inflation.
Design Flaws
Poor design choices can increase the likelihood of belly inflation. For instance, inadequate wall thickness or incorrect material selection may lead to structural weaknesses. Engineers must ensure that equipment is designed to withstand the pressures it will encounter during operation.
Material Degradation
Over time, materials used in industrial equipment can degrade due to exposure to harsh conditions. Corrosion, erosion, and fatigue are common culprits of material degradation, which can weaken the structural integrity of components and make them more susceptible to belly inflation.
Read also:Crowned In Love The Mother Of Three Who Inspires Millions
Operational Errors
Human error during operation can also contribute to belly inflation. Overpressurization, improper maintenance, and inadequate monitoring are examples of operational errors that can lead to this phenomenon. Training and adherence to best practices are essential for minimizing these risks.
Effects on Industrial Systems
Belly inflation can have far-reaching effects on industrial systems. These effects include reduced efficiency, increased downtime, and higher maintenance costs. Additionally, the safety risks associated with belly inflation can lead to regulatory violations and reputational damage.
Reduced Efficiency
When equipment experiences belly inflation, its performance can be severely impacted. Deformed components may no longer function as intended, leading to inefficiencies in the production process. This can result in decreased output and increased costs for businesses.
Increased Downtime
Addressing belly inflation often requires equipment to be taken offline for inspection and repair. This downtime can disrupt operations and delay project timelines, further impacting profitability. Preventive measures are therefore crucial for maintaining operational continuity.
Higher Maintenance Costs
The costs associated with repairing or replacing equipment affected by belly inflation can be substantial. Regular maintenance and inspections are necessary to identify potential issues before they escalate, helping to control these costs.
Prevention and Mitigation
Preventing and mitigating belly inflation requires a proactive approach. This includes implementing robust design practices, conducting regular inspections, and utilizing advanced monitoring technologies.
Robust Design Practices
Designing equipment with belly inflation in mind is critical for preventing this phenomenon. Engineers should consider factors such as material selection, wall thickness, and pressure ratings to ensure that components can withstand operational stresses.
Regular Inspections
Regular inspections are essential for detecting early signs of belly inflation. Visual inspections, ultrasonic testing, and radiographic analysis are some of the methods used to assess the condition of industrial equipment. Early detection can prevent minor issues from becoming major problems.
Advanced Monitoring Technologies
Advancements in technology have made it possible to monitor industrial systems in real-time. Sensors and data analytics can provide valuable insights into equipment performance, allowing operators to address potential issues before they lead to belly inflation.
Technological Advancements
Technology plays a vital role in addressing belly inflation on industrial systems. Innovations in materials science, monitoring systems, and predictive analytics have significantly improved the ability to prevent and mitigate this phenomenon.
Innovations in Materials Science
New materials with enhanced strength and durability are being developed to withstand the rigors of industrial applications. These materials can help reduce the likelihood of belly inflation by providing greater resistance to pressure and environmental factors.
Real-Time Monitoring Systems
Real-time monitoring systems enable operators to track the performance of equipment continuously. By analyzing data from sensors and other sources, these systems can identify potential issues before they escalate, allowing for timely interventions.
Predictive Analytics
Predictive analytics uses historical data and machine learning algorithms to forecast equipment failures. This technology can help predict when belly inflation is likely to occur, enabling proactive measures to be taken to prevent it.
Industrial Case Studies
Examining real-world examples of belly inflation can provide valuable insights into its causes and effects. Case studies from various industries highlight the importance of addressing this issue and the benefits of implementing effective prevention strategies.
Case Study 1: Oil and Gas Pipeline
In one instance, an oil and gas pipeline experienced significant belly inflation due to overpressurization. The subsequent failure resulted in a major spill, causing environmental damage and financial losses. This case underscores the need for robust pressure management systems.
Case Study 2: Chemical Storage Tank
A chemical storage tank suffered from belly inflation after years of exposure to corrosive substances. The resulting deformation led to leaks and safety concerns. Regular inspections and maintenance could have prevented this incident.
Regulatory Standards
Regulatory standards play a crucial role in ensuring the safety and integrity of industrial systems. Compliance with these standards is mandatory for businesses operating in regulated industries, and non-compliance can result in severe penalties.
Key Regulations
Regulations such as ASME Boiler and Pressure Vessel Code and ISO standards provide guidelines for designing, manufacturing, and maintaining industrial equipment. Adhering to these standards helps mitigate the risks associated with belly inflation.
Importance of Compliance
Compliance with regulatory standards not only ensures safety but also enhances the reputation of businesses. Companies that prioritize compliance are more likely to gain the trust of customers and stakeholders, leading to long-term success.
Economic Impact
The economic impact of belly inflation on industrial systems can be significant. From repair costs to lost productivity, businesses must account for the financial implications of this phenomenon. Effective risk management is essential for minimizing these impacts.
Repair and Replacement Costs
Repairing or replacing equipment affected by belly inflation can be costly. Businesses must factor these costs into their budgets and implement preventive measures to reduce the likelihood of incurring such expenses.
Lost Productivity
When equipment is taken offline for repairs or inspections, productivity suffers. This downtime can have a ripple effect throughout the supply chain, leading to delays and increased costs. Preventive maintenance can help maintain productivity levels.
Safety Protocols
Safety protocols are essential for protecting workers and equipment from the dangers of belly inflation. These protocols should be clearly defined and communicated to all personnel involved in industrial operations.
Training and Education
Training employees on the risks and prevention of belly inflation is crucial for ensuring safety. Workers should be educated on proper operating procedures, inspection techniques, and emergency response protocols.
Emergency Response Plans
Having a well-defined emergency response plan in place is essential for addressing incidents of belly inflation. This plan should outline the steps to be taken in the event of a failure, including evacuation procedures and containment measures.
Future Trends
The future of belly inflation prevention lies in the continued advancement of technology and the adoption of innovative solutions. As industries evolve, so too must the strategies used to address this critical challenge.
Emerging Technologies
Emerging technologies such as artificial intelligence, machine learning, and the Internet of Things (IoT) hold great promise for improving the prevention and mitigation of belly inflation. These technologies can enhance monitoring capabilities and enable more accurate predictions of equipment failures.
Sustainability Initiatives
Sustainability is becoming increasingly important in the industrial sector. Businesses are exploring ways to reduce their environmental impact while maintaining operational efficiency. Addressing belly inflation through sustainable practices can contribute to this goal.
Kesimpulan
Belly inflation on industrial systems poses significant risks to safety, efficiency, and profitability. By understanding its causes, effects, and prevention strategies, businesses can take proactive steps to mitigate these risks. Implementing robust design practices, conducting regular inspections, and utilizing advanced technologies are key to addressing belly inflation effectively.
We encourage readers to share their thoughts and experiences in the comments section below. Additionally, feel free to explore other articles on our site for more insights into industrial safety and innovation. Together, we can work toward a safer and more sustainable future for the industrial sector.
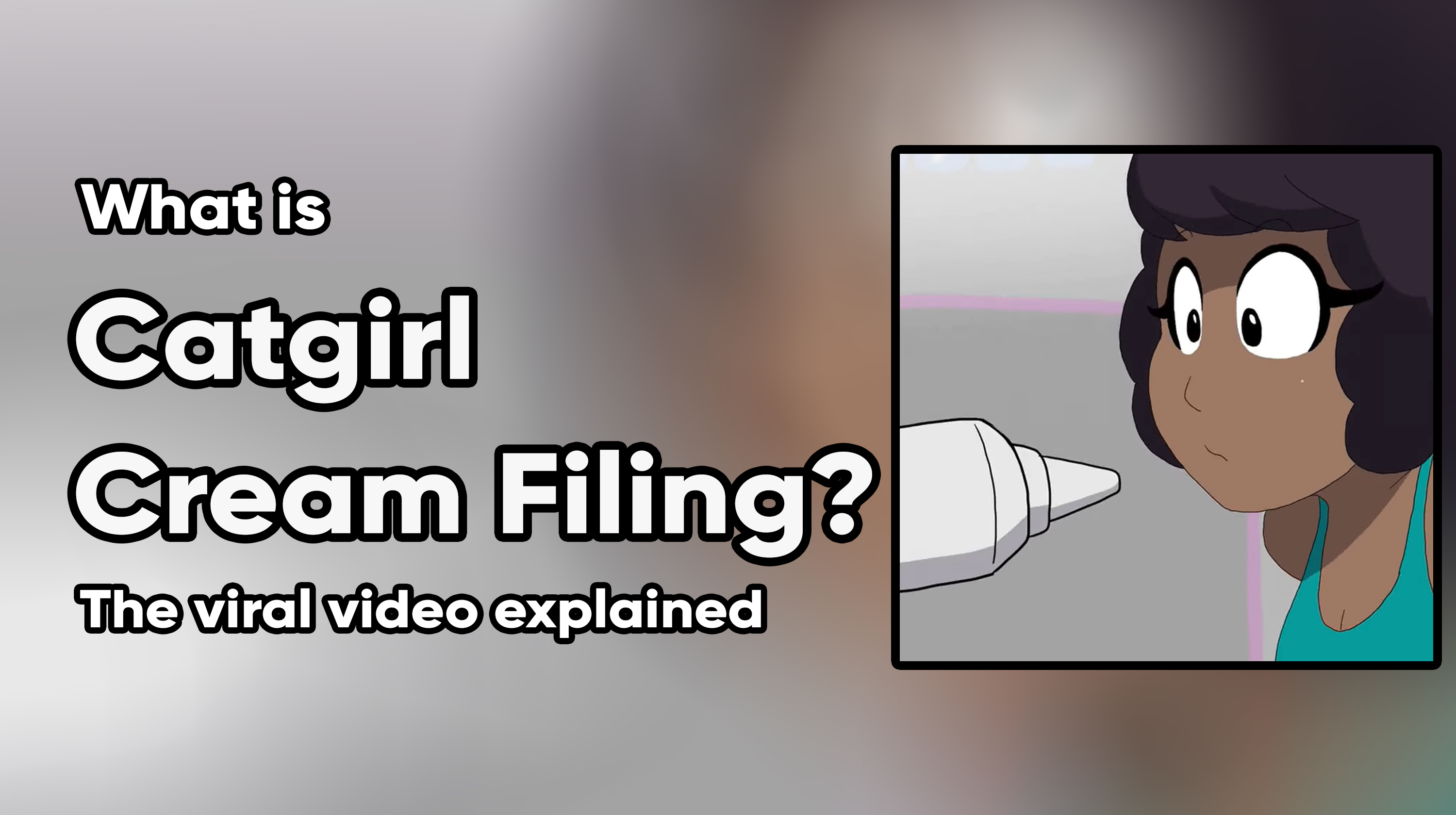

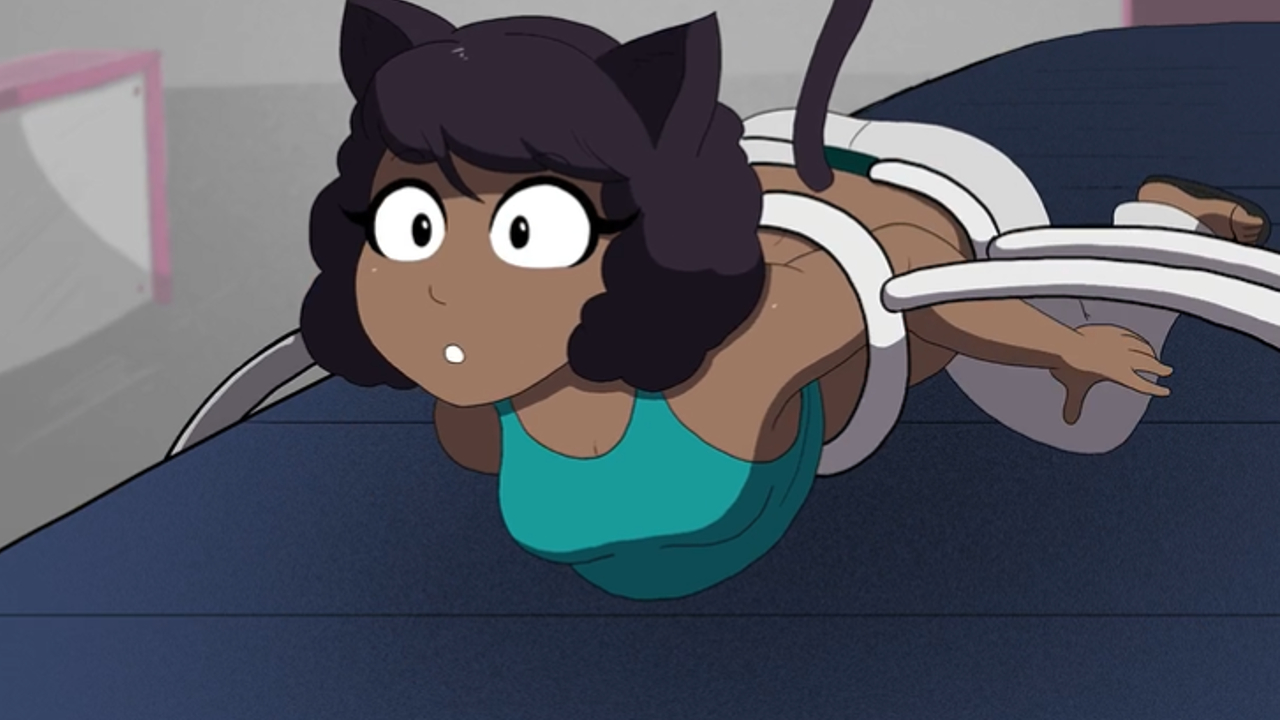